Constructing Ship Sections
The newbuilding of ship’s sections, ship’s hulls and ship’s superstructures for megayachts, cruise ships, naval vessels and specialized vessels, even up to many thousands of tons in weight, has been one of our core competencies for decades.
In most cases, we cover the complete steel construction from the keel to the funnel for our customers.
Base Section - Steel - Cruise Ship - 1.100 Tons - 2019
The pictured base section, weighing in at 1.100 tons, was built as shown at our site in Bremen, Zur Westpier 40, in January 2019 and again in September 2019
The stabilizers which are fitted into this section both on starboard and on portside prevent the rolling of the cruise ship (=rotation along the longitudinal axis) and are meant to protect the passengers from sea sickness.
The base section was moved by self-propelled modular transporters (SPMTs) from the construction hall to the pier and onto the pontoon of our sister company BVT Chartering und Logistics. It was then transported on the river Weser to our customer.
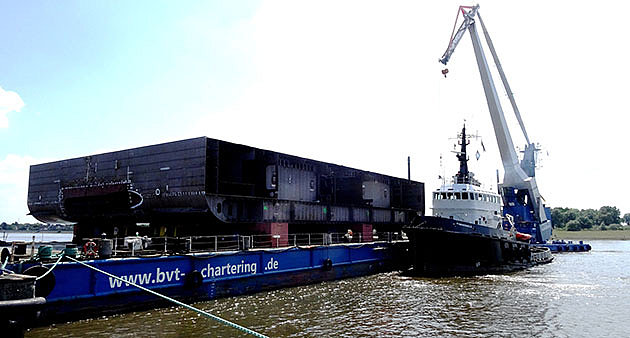
Forecastle, Midship and Stern - Steel - Megayacht - 4.000 Tons - 2018
We used approximately 4.000 tons of steel for the newbuilding of a megayacht in 2017/2018.
The individual sections were built at our site in Bremen and moved across the Weser to the Lune Hall in Bremerhaven by barge or barge crane in 2017 and 2018. There, the sections were built into blocks and, afterwards, three large blocks.
Upon completion, the forecastle, midship and stern were moved by self-propelled modular transporter (SPMTs) from the Lune Halle to the heavy-duty barge “Offshore BHV 1” and transported to the customer by our sister company BVT Chartering und Logistics.
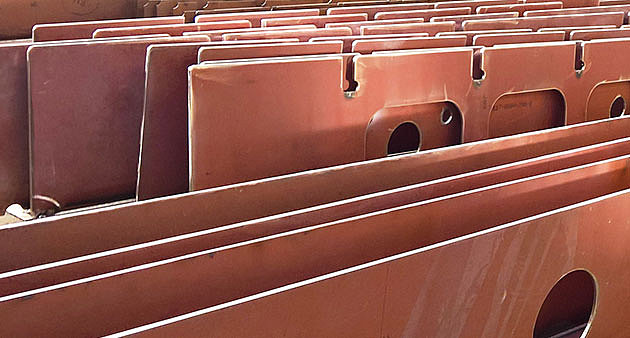
Midship - Steel - Lengthening of a Ferry - 1.300 Tons - 2016
When cruise ships, ferries, tanker vessels or refrigerated vessels grow to short to be operated profitably, the lengthening of a ship presents a good alternative to a complete newbuilding for ship owners.
In the picture you can see an extension section, 30 meters in length and 20 meters in width, for a ferry, which we lengthened for a customer in 2016.
The midships section, weighing in at 1,300 tons, was built in the Lune Halle and transported onto the heavy duty barge “Offshore BHV 1” operated by our sister company BVT Chartering und Logistics on the heavy duty rail-system which is integrated in the Lune Halle.
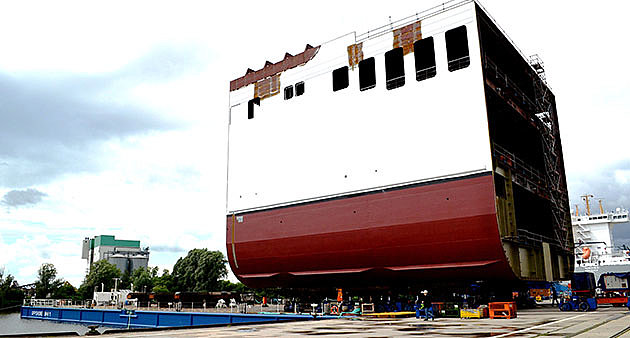
Foreship and Aft Section - Steel - River Cruise Ship - 2016
The cruise industry in international waters is growing steadily. But the same is true for the demand for luxurious river cruise ships, especially for cruises on European rivers.
While river cruise passengers used to be happy with few amenities, the modern design of river cruise ships is inspired by the design of private yachts. Open spaces flooded by light, roomy suits, gourmet restaurants, as well as pool, spa and gym areas are perfectly normal luxuries today.
In 2015 and 2016, we built a total of four foreship and aft sections for river cruise ships, which today operate on the Rhine, Main and Danube rivers.
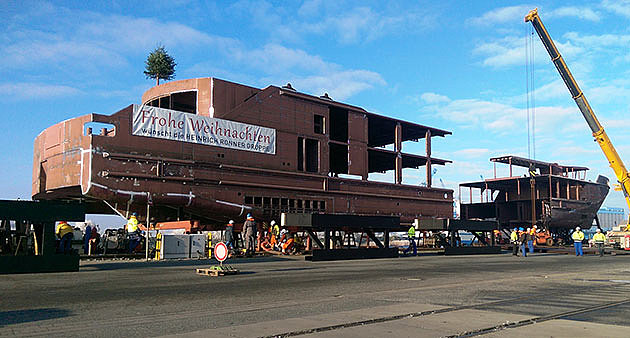
Superstructure - Aluminum - Megayacht - 2015
In 2015, we built the aluminum superstructure for a mega yacht almost 100 meters in length, which you can find pictured here.
We built the superstructure at our premises in Neufundlandstraße and transported it with the help of the barge crane “BHV Athlet” to the floating dock of our sister company BREDO DRY DOCKS, where it was joined with the stele hull.

Ship's Hull - Steel - Megayacht - 2014
We delivered the pictured steel hull for a yacht to our customer after a building time of nine months.
The 72-meter-long hull, which was completely built at our site in Neufundlandstraße, is among the shorter editions for modern mega yachts.
At our premises in Neufundlandstraße, we are able to build hulls of up to 85 meters in length and transport them by sea to our customers.

Ship's Hull - Steel and Aluminum - Megayacht - 2013
The 82-meter-long mega yacht, for which we built the hull from steel and aluminum in 2013, is still among the world’s 100 largest megayachts today.
By established procedure, the hull was transported out of the construction hall on SPMTs and set into the water with a heavy-duty vessel.
The mega yacht hull was then transported to the customer by tug-boat – on its own buoyancy.
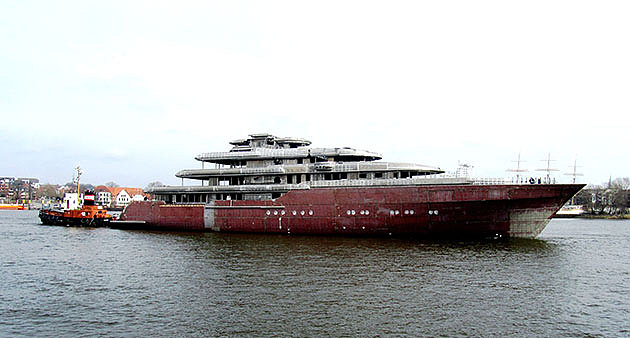
Ship's Hull - Steel - Megayacht - 2012
In 2012, we did not only build the hull for the 82-meter-long mega yacht – we also built the aluminum superstructure of the same vessel.
The steel hull was moved out of the construction facility in Neufundlandstraße on SPMTs. It was set in the water by a heavy-duty vessel and transported to the customer by tugboat on its own buoyancy.
The aluminum superstructure was attached to the hull at a later time at the shipyard which also completed the outfitting of the vessel.
Ship's Hull - Steel - Megayacht - 2010
This ship’s hull, which is in the process of being set in the water by the pontoon crane “Enak”, is almost 80 meters long.
The hull was constructed in one piece at our premises in Neufundlandstraße in 2010 and was transported from the construction hall on SPMTs.
The hull of a mega yacht was transported to the customer on its own buoyancy.
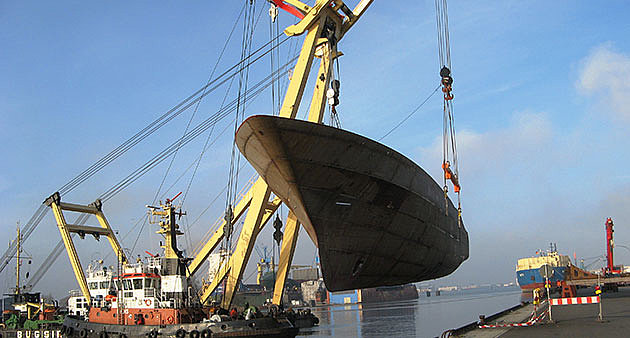
Superstructure - Aluminum - Megayacht - 2010
The aluminum superstructure for this 60-meter mega yacht was constructed at our premises in Riedemannstraße in Bremerhaven in 2010.
After construction was finished, the superstructure was moved from the construction hall and across the former Seebeck-site to the pier by SPMT.
Form there, it was transported to our site at Neufundlandstraße by barge crane, where it was attached to the hull constructed on-site.
Ship's Hull - Steel and Aluminum - Megayacht - 2009
The steel hull for the 78-meter-long mega yacht was constructed at our large section construction site in Bremen in 2009 and transported to the pier by SPMT. It was set into the water by the pontoon crane “Enak”.
The aluminum superstructure for the hull was constructed at our sites in Bremerhaven and transported to our sites in Bremen at Zur Westpier 40 by floating barge.
The aluminum superstructure sections were set onto the steel hull with the help of the floating crane “Enak”. The full construction was then moved to the outfitting shipyard on the Weser river –on its own buoyancy.
Ship's Hull - Steel and Aluminum - Megayacht - 2009
From 2007 to 2009, we constructed a ship’s shell (ship’s hull built from steel, superstructure built from steel and aluminum), weighing in at 2,300 tons for a 115-meter-long mega yacht. At this size it is still among the world’s 30 largest mega yachts today.
The sections of the ship shell were constructed via a joint effort of all company facilities and, additionally, using several facilities of the HEINRICH RÖNNER GROUP. Piece by piece, they were delivered to the dry dock of the outfitting shipyard, where they were combined into one ship shell. Transportation of the individual sections happened in many different ways, by barge crane and floating barge; smaller sections were also transported by truck.
We completed this project all on our own, including the construction and transport logistics, until it was handed over to the outfitting shipyard.
Ship's Hull - Steel - Swath Style - 2009
In 2009, we built a SWATH (Small Waterplane Area Twin Hull)- style steel ship’s hull. Vessels, which are equipped with such a twin hull and two underwater torpedo-shaped flotation panels, are especially resistant to sea swell.
The ship platform, which stays over the water, was built at our site in Bremerhaven. The two torpedo-shaped flotation panels were built by one of our sister companies, the Roßlauer Schiffswerft.
The final assembly of the floatation panels, the platform and the superstructure was done by us onsite at our sister company BREDO DRY DOCKS in Bremerhaven. We completed a total of three SWATH-style ship hulls made from steel and six smaller hulls made from aluminum between 2009 and 2011.
Superstructure - Aluminum - Megayacht - 2008
An aluminum superstructure with a futuristic design was constructed by us at our Neufundlandstraße site in Bremerhaven in 2008. The superstructure is part of a 95-meter long megayacht, which is among the world’s 50 largest megayachts.
The aluminum superstructure was constructed in two parts and was, following a conforming request by the customer for secrecy reasons, transported on a floating barge whilst completely wrapped in foil.
The final attachment of the superstructure to the ship’s hull was done by us in dock at the outfitting shipyard.
Superstructure - Aluminum - Megayacht - 2008
An aluminum superstructure, built by us in 2008 for a 78-meter-long mega yacht, was constructed in one piece at our premises in Neufundlandstraße.
The superstructure was transported from the construction hall by the integrated heavy load rail system and set onto the waiting hull by way of the floating crane “Athlet”.
The final assembly was done by us in the dock at the outfitting shipyard.
Ship's Hull - Aluminum - Megayacht - 2007
On site at our premises in Riedemannstraße 3, Bremerhaven, we built an aluminum superstructure for a 78-meter-long megayacht on 2007.
The superstructure was transported to our premises at Neufundlandstraße by way of the floating crane “Athlet”, where it was joined with the awaiting hull.
The steel hull and the aluminum superstructure were welded together by us on site at the dock of the outfitting shipyard.
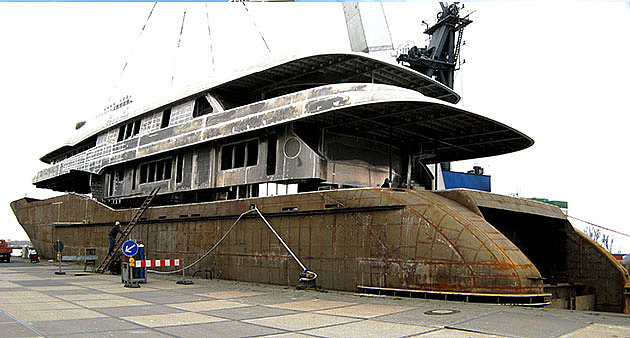
Ship's Hull - Steel - Megayacht - 2005
Even though we are able to build hulls up to length of 85 meters in one piece at our premises in Neufundlandstraße, this 68-meter-long steel hull was built in two pieces in 2005.
The first step: the aft section was moved out of the construction hall with the integrated heavy load rail system and transported to the floating dock at the site of our sister company BREDO DRY DOCKS with the help of the pontoon crane “Enak”. The second step: the foreship section was transported in the same way, after which both parts were welded together by us in the dock.
After undocking, the hull was transported to the customer on the seaway – swimming on its own.